Bike frame material: everything you need to know
How does each bike frame material differ and will it affect more than just your bank balance?
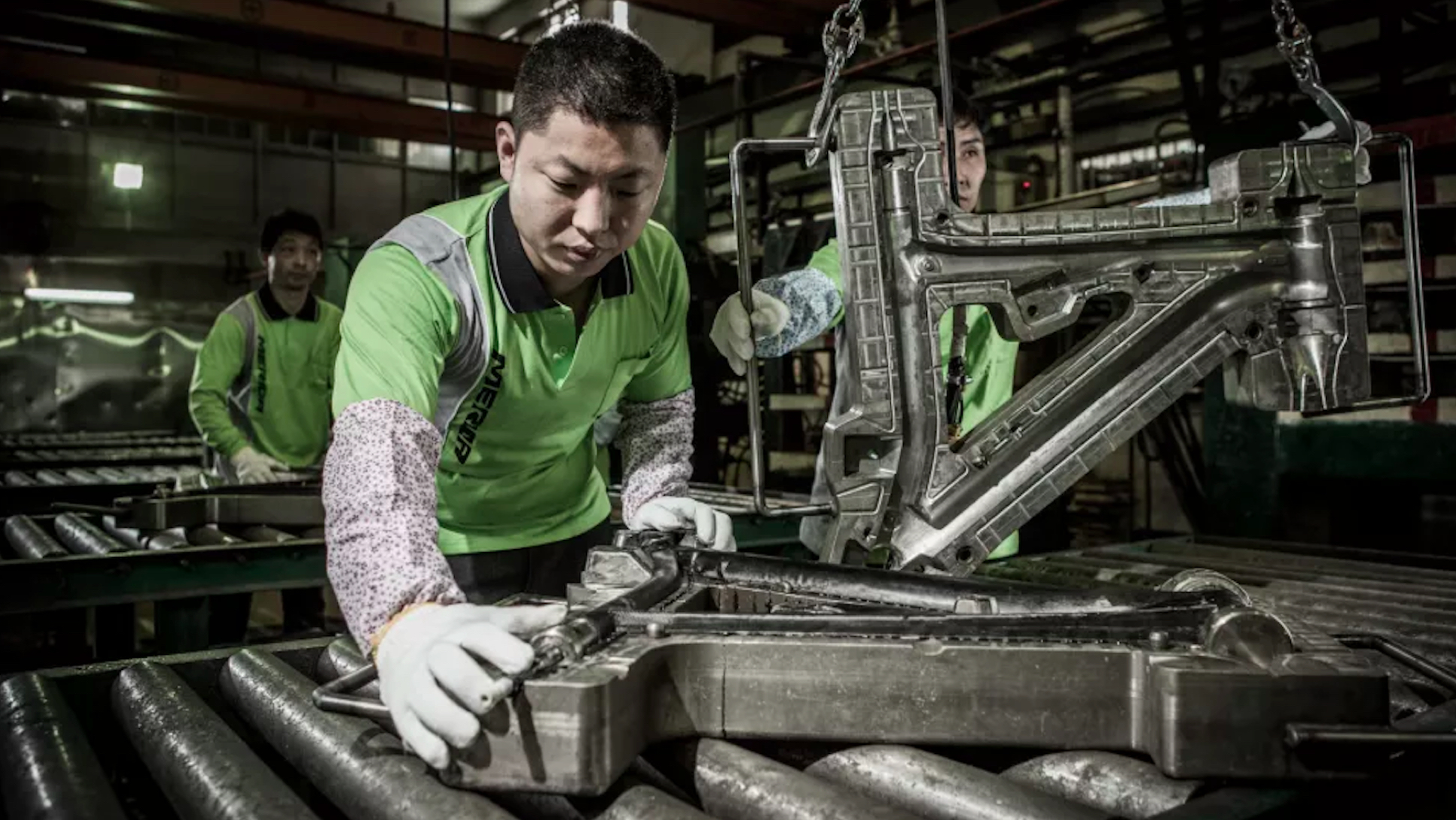
A major factor in deciding what bike you want to buy is the bike frame material. Back in the early days steel was the only choice. These days there are a number of different options. Each choice has different characteristics with regards to the overall “feel” of the frame – its stiffness, its weight, even its effect on the aesthetics of the bike.
The choice of material will largely depend on your budget and the intended use. Whether you want the best mountain bike or best gravel bike for your needs (or budget), it can be tricky to determine which bike frame material is the best option for you.
Fear not, we’ve made a list here that should help, whether you’re a first-time buyer or it's time to cough up and payout on a new steed.
Tubular talk
Essentially the larger the tube diameter used to make the frame, the greater the stiffness of the tube and frame. But as the diameter begins to increase, so will its weight. To counter this, engineers use thinner-walled tubes to reduce some of this additional mass but to keep the desired amount of rigidity and stiffness in the frame’s construction. It’s a neat trick but it’s a fine line. Make the tube wall thickness too thin and you can expect a lightweight bike but one that could be susceptible to buckling or be easily damaged.
Tubes can be straight-gauge, single-, double- or even triple-butted. Straight-gauge tubes have the same constant thickness throughout the length. Butted tubes have greater thickness at the ends where there is likely to be more stress – such as at joints with another tube – and then thinner on the middle to save weight. Typically, as the amount of steps in the thickness increases as does the strength and stiffness.
Different parts of the frame will require a different tube-wall thickness to give the optimum stiffness and tweaking this in multiple areas of the bike will help tune the frame and its ride characteristics. You want a tube material that will absorb greater levels of energy before failing and allowing the material to flex and bend rather than just snapping. Compliance or flex in areas like seatstays of a fully rigid gravel bike will add a level of comfort for longer days in the saddle absorbing trail buzz, and the use of stiffer grades in high-stress areas (head tube) and with multiple joints (bottom bracket shell).
Tuning a frame and adjusting wall thicknesses is one way, but also changing the material to a different grade for particular sections of the frame will also alter the feel of a bike. Each choice of frame material has its own properties and stiffness. Stiffness is the ability of any given material to return back to its original shape after it has undergone loading (not to be confused with material strength).
Steel
Steel is where it all began for bike frame materials and it remained that way almost exclusively until the 1990s with the emergence of aluminum alloy. Steel alloy frames are constructed traditionally with round tubes. The tubes can be joined using welding or brazing techniques or by the use of lugs (tubes slotting into open socket joints and then brazed).
The base grade is typically 4130 and the ratio of ingredients that make up the alloy can be tweaked. The various grades have different properties; some higher-quality steel frames use a mixture of grades in different areas of the frame to tune the feel of the bike. The material can be treated by a process of both heating and cooling using a variety of techniques. Reynolds is the master, offering butted tubing in everything from its new annealed stainless 953 “Super Steel” to a competitively priced 520 Chrome-Moly and many more between.
There is a reason steel alloy frames were the popular choice for so long and why frame builders and manufacturers still love the stuff. The material is relatively easy to work with, durable and resilient and it can be repaired when bent or damaged. The feel of a steel-framed bike is something you have to experience, it’s naturally springy and compliant to ride.
It’s not all gravy though. Steel alloy frames are typically heavier and also more expensive to produce than aluminum alloy frames. Also, if left damaged or neglected, steel alloy bikes will corrode in time. Be wary of mixing steel frames with aluminum components, such as seatposts – without proper care and attention, over time the two materials can corrode themselves together.
Pros
• Offers springy and comfortable ride
• Can be repaired
• Durable strength
Cons
• More expensive than aluminum alloy
• Weight penalty
• Could rust if neglected
Aluminum alloys
When aluminum alloy burst onto the cycling scene in the 1990s it was often marketed as an aerospace or even space-age material. It’s lightweight and with impressive stiffness. These days aluminum alloy frames tend to prop up the more affordable end of the bike frame market through to mid-range bikes. But don’t be fooled into thinking this is just a budget frame material; the UK’s own Orange mountain bikes is infamous for its use of monocoque aluminum tubing with a range of full-suspension bikes.
The most commonly used grades of aluminum alloy material for bike tubing are 7005 and 6061. Generally, 6061 aluminum is solution-heat treated, then aged. T4 temper aluminum is naturally aged, and T6 temper aluminum is artificially aged. So with 6061 T6 aluminum alloy, the material is heat-treated to further maximize its strength properties. Heat treatment is an important process. It helps to relieve material stress after welding and it can affect tensile strength and ductility properties while leaving the material’s stiffness unchanged.
Aluminum’s formable properties and low density (especially 6061) mean that manufacturers can work the material into more intricate shapes than steel alloys. The process is called hydroforming. The aluminum alloy material is shaped by injecting pressured oil into the tubing and forcing it outwards in a mold. This means that the higher-end frames can be made into almost any shape, and even be aerodynamically similar to carbon fiber. The process also allows frame details to be formed into the tube to cut down welding whilst maintaining the desired wall thickness and strength.
Aluminum is a more brittle bike frame material than steel and this usually means that there is more material required for a similar stiffness. Aluminum alloy tubing is thicker and oversized to compensate but is still lighter than steel alloy. Unfortunately, it can be prone to fatigue over long periods of time and it is not easy to repair once damaged.
There have been other more unusual methods using aluminum for bike frames in the past. The Empire Cycles AP-1 took casting technology from the world of motocross to produce a mountain bike, albeit one a tad on the portly side.
Pros
• Lightweight
• Cheaper
• Excellent performance when executed well
Cons
• Not easy to repair like other alloys
• Cheapest frames produce a harsher ride
• Material fatigues
Titanium alloy
Titanium alloy is the exotic choice of frame fabricators. Its properties are super desirable in bicycle frame application but it is going to hurt your bank balance. It is considered a rarer metal to source, causing the price to rise dramatically over the other metal material options here. Also hiking the price above some riders’ budgets is the fact that titanium alloy has exceptional resilience to fatigue under repeated stresses thus making it more difficult to work with. These same fatigue-resistance properties also mean less material is required, making the finished frame lighter and with greater ride characteristics.
Titanium alloy is similar to the other metals in that there are different grades available to manufacturers. The ingredients that make up the alloy can be tweaked for the particular properties that are most desirable for the given application. The cocktail of additional ingredients is usually aluminum and vanadium. A common grade is AL3 2.5V, but for areas of the frame that require more stiffness sometimes a more expensive 6AL 4V grade is selected.
With similar ride characteristics to steel, titanium’s natural flex provides a smooth ride and with the right skills can be repaired if damaged during a crash. It is resistant to corrosion, which means that its smaller diameter tubing can be left unpainted in its beautiful raw color. It is also considerably lighter than steel. All these perks will really cost, with some titanium frames prices higher than carbon fiber counterparts. If you consider that a titanium frame could be your frame for life, that makes the hefty cost a little easier to swallow.
Pros
• Lightweight tubing
• Corrosion-resistant and strong alloy
• A frame for life that won’t fatigue
• Best ride quality
Cons
• Difficult to work with
• High material cost
Carbon fiber
Carbon fiber occupies the top end of the bike frame market. It’s the magic material that can be found all over modern Formula 1 cars. Most bikes on the race scene of any cycling discipline are made using carbon fiber.
Typically carbon fiber is lighter than any other frame material. The other major perk is that flex and stiffness can be engineered into the frame. The frame can be made to meet the demands of a particular use, making a bike super stiff for road racing or adding compliance to enhance comfort. Frames can be molded into almost any complex shape.
It is constructed using layers of fibers that are fused by a matrix of epoxy resin. Most frames use a technique called “prepreg”. The many sheets of fibers have already been impregnated with resin and are ready to be layered into a mold to be formed using a combination of heat and pressure. The number of layers and the direction of the fibers change the stiffness of the frame.
The two main types of frame construction are monocoque or the tube-to-tube method, which is similar to lugged alloy frames. Preformed tubes are bonded into molded lugs at junctions on the frame. The type of carbon fiber used will affect the characteristics and the price. Bike frames can be molded using a stiffer high-modulus grade to make a frame lighter and stiffer, but the trade-off is that this makes it brittle, so a mixture of grades is utilized. Some manufacturers are using additives in the resin to tweak the properties of their carbon fiber frames.
Carbon fiber cannot have a thread taped or screwed into it, so metal will need to be bonded into areas like the bottom bracket shell (added weight) or bearings require a tolerance fitment. Press-fit bottom brackets have a reputation for being noisy and if bonded metal shells are not square you can expect component fitting issues potentially rendering a frame useless.
The mold for a monocoque carbon fiber frame can cost a substantial amount of money, making sure that there are no defects or issues with the design is crucial before putting the mold into full production. A different mold would be required for each different frame size. While the price has reduced somewhat in recent years, this cost is passed onto the consumer, hence why it is only used on the most expensive bike frames.
Another major downside is that while it has the highest strength-to-weight ratio, carbon fiber’s strength is only in the one direction; the material can be damaged more easily than metal frames and once fractured its difficult to repair.
Pros
• Lightweight
• Can be made into complex shapes
• Compliance can be designed into the lay up
Cons
• Susceptible to damage
• Cost
Other options
Grass? Really? Yes, you read that right. Bamboo (which is, in fact, a variety of grass) has been successfully used as a bike frame material for some time now. You have very limited options with only specialist companies choosing this as a material to work with.
Scandium can be paired with aluminum to make an alloy and magnesium alloy has been used. Despite offering some desirable properties in regards to weight and compliance, neither of these materials are widely used in the industry due to do demand, complications of manufacture and cost.
The final word
There is no one material that does it all perfectly; there will always be a compromise. They are all great in multiple ways but they all have their own drawbacks. So my advice here is to align the material that suits your requirements the closest.
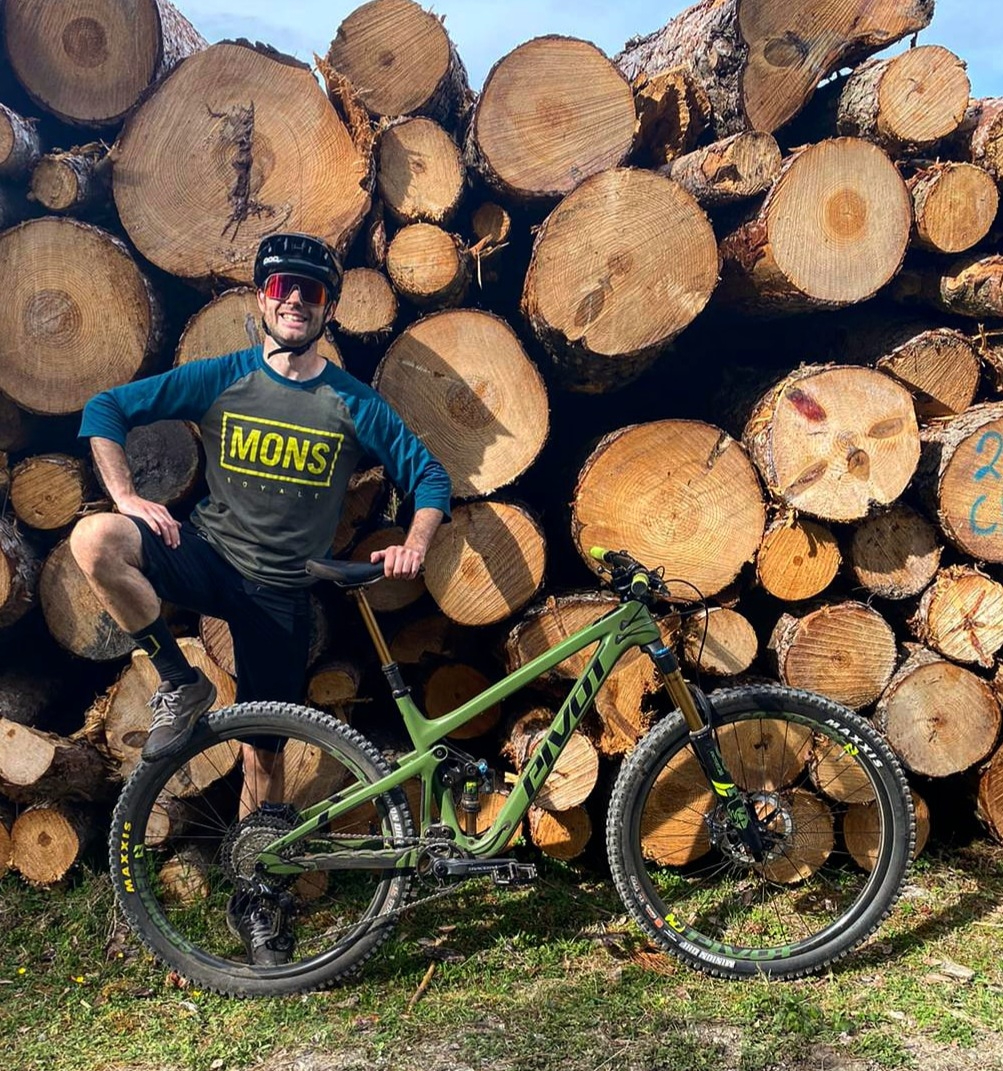
Dean is a freelance cycling journalist and a self-confessed pedal addict based in Dorset, who's fortunate to have the New Forest National Park and the Isle of Purbeck on his doorstep. Not confined to his local spots, riding bikes has meant Dean has been fortunate to travel the world in search of the best trails. From summers spent in the Alps to exploring iconic locations such as Scotland, Aosta Valley, the Pyrenees, Finale Ligure, New Zealand and Whistler to name a few. Over the years he has dabbled in racing DH and enduro to XC. More recently Dean has been exploring the UK with his gravel bike and loves a bikepacking trip. As passionate about writing as much as his riding, by recapturing his adventures through his stories and sharing his own experiences of products by writing technical reviews, he's also a regular contributor for Singletrack and Grit CX.
Rides: Open U.P
Height: 180cm
Weight: 65kg